The COVID-19 pandemic created unprecedented disruptions across manufacturing supply chains. For American injection molding companies relying on suppliers and materials from China and other countries, shortages and delays seriously impacted production. With the crisis illuminating vulnerabilities, manufacturers were forced to make changes to protect their supply networks.
As the industry continues recovering, companies are building resilience for the long-term. Strategic shifts enacted during COVID-19 will shape more agile, localized, and transparent supply chains. Here are some of the ways the pandemic changed injection molding’s sourcing landscape.
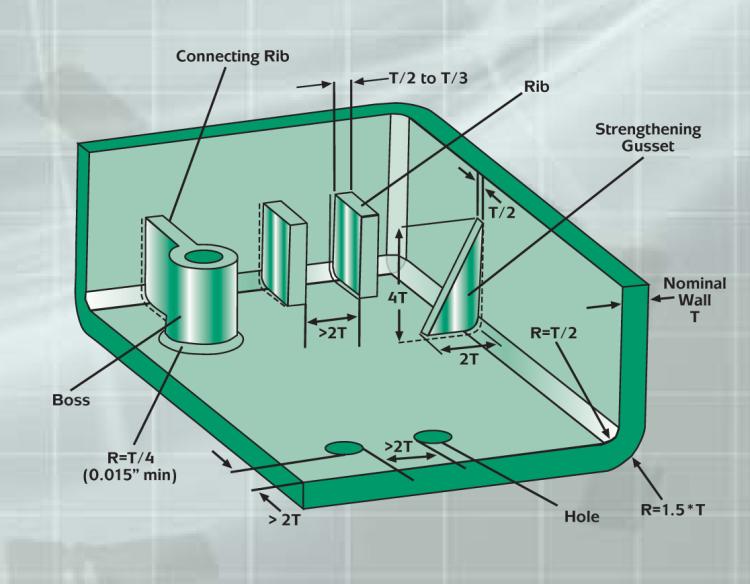
Exposing the Risks of Long Supply Chains
In pre-pandemic times, injection molders commonly imported molds from China and bought raw plastic resins on the spot market to get lowest prices. While economical, the extended supply lines and just-in-time inventory left companies exposed. Once trade flows stalled in early 2020, shortages rapidly emerged.
With containers trapped at ports, companies lacked materials to meet production schedules. Air freight costs spiked ten-fold, making emergency transports unfeasible. Faced with no choice but to halt production, some companies lost major orders and revenue.
The crisis illuminated hidden fragilities in extended offshoring and lean inventory strategies. The drive to cut costs through globalized sourcing created unintended risks. Companies learned the hard way the downsides of relying on distant suppliers and keeping minimal stock.
Diversifying Supply Chains Across Regions
Rather than relying on single suppliers, manufacturers now diversify sourcing to reduce geography risk. A portfolio of vetted partners across different regions provides insurance if one area faces lockdown restrictions or transport snarls.
Building supply relationships closer to home also enables flexibility. For instance, some companies shifted to mold makers in Mexico due to delays from China. Having regional suppliers to turn to avoids potential catastrophic shutdowns.
Diversification provides redundancy and flexibility to adapt to black swan events. Spreading molds and materials across suppliers in North America, China, Europe, and Southeast Asia mitigates over-reliance on any one source.
Localizing Production and Sourcing
The supply instability accelerated moves to reshore and localization. Forty percent of low volume injection molding companies surveyed expect to onshore more production post-pandemic. This mirrors wider reshoring trends across industries.
Sourcing more molds and materials from domestic suppliers reduces risks inherent with global transport. Local also enables greater oversight and collaboration. several injection molders bought machines to bring mold production in-house for faster iteration.
Localizing raw materials, packaging, and tooling provides a buffer against offshore turmoil. geographic clusters epitomized by Silicon Valley maximize efficiencies between connected manufacturers, suppliers, and partners in one region.
Building Inventory Buffers
After running out of key supplies during the crisis, lacking even basic items like labels and resin pellets, companies now maintain larger safety stocks. Buffered inventories prevent scramble situations when facing unforeseen events.
Stockpiling extra months of critical mold components, maintenance parts, and inputs provides insurance until supply flows stabilize after disruptions. The costs of holding inventory is now viewed as less than the crippling impact of shutdowns.
Manufacturers also diversify warehouses across regions to avoid potential local restrictions. Balancing efficiency and resilience remains an art, but the crisis shifted mindsets on inventories.
Transparency Through Supply Chains Digitization
Limited visibility into offshore supplier operations compounded problems. Companies with software integrating procurement, orders, inventory, and shipments had advantages responding to shortages.
Supply chain digitization is bridging information gaps through sensors, IoT, and shared data platforms. This enables real-time tracking, proactive risk management, and predictive analytics.
For instance, cloud-based supply chain control towers provide holistic visibility across every supplier tier. Automated inventory management software helps optimize stock levels. Digital tools promote transparency and rapid response.
Closer Supplier Relationships and Communication
The disruptions demonstrated the need for suppliers to be trusted partners, not just vendors. Strong relationships enabled greater flexibility and mutual support when pressures mounted.
Injection molders are nurturing closer ties with strategic suppliers based on open communication and shared plans. Multi-year contracts offer volume commitments while pooling risks. Things like joint contingency planning, forecasting, and R&D collaboration promote transparency.
Nurturing trust and interdependence with top suppliers improves resilience. This reduces misalignments and enables quicker reactions to deviations. Both sides are invested in mutual success.
Agility Supply Chains Through Standardization
Design standardization emerged as a strategy for managing supply uncertainty. Parts and molds that conform to industry standards are more interchangeable across different vendors when necessary.
Standardized components also streamline production planning and modifications when facing shortages. Rather than fully custom designs, modularized solutions using common standards, interfaces, and guidelines provide more adaptability.
Shared standards enable flexibility across the production ecosystem. Standardizing digital supply chain data and metrics also facilitates visibility and seamless integration when needing to shift suppliers.
Dual Sourcing Key Inputs
Despite closer supplier relationships, injection molding companies now use dual sources for vital supplies as a rule. Even the best partners may be impacted by forces outside their control.
Maintaining backup suppliers and material streams prevents severe disruption if one source falls through. Having overlapping suppliers and pre-qualified alternates provides failover options to guarantee continuity.
While managing two supply chains entails added effort, the pandemic proved that redundancy is essential insurance. Dual sourcing critical mold components, resins, chemicals, and packaging protects output.
Emphasizing Supply Chains Domestic Workforce Development
Supply uncertainty increased focus on developing domestic technical talent. Travel restrictions limited ability to bring in offshore experts to fill skills gaps.
Manufacturers are partnering with trade schools, community colleges, and universities to build local workforces. Apprenticeships and in-house training enable growing talent organically.
Having readily available local teams able to operate advanced manufacturing equipment ensures resilience. Rather than depending on outsiders, skilled regional workforces confer adaptability.click for more
Conclusion
While initially painful, the pandemic made the China plastic molding industry wiser about supply chain risks. The acute shortages forced manufacturers to strengthen their sourcing models for the long-haul.
Localizing production, digitizing supply chains, managing inventories, and nurturing supplier relationships are positive changes. Reliance on any single source or country is fading.
Adaptable, transparent supply networks will be vital in the years ahead. By learning important lessons, American injection molders are positioning themselves to better handle the next crisis.