In an era increasingly dependent on battery-powered devices—from electric cars to renewable energy systems—the focus on battery safety and sustainability has never been more critical. For years, manufacturers have grappled with issues such as overheating, leakage, and short lifespan. Traditionally, mechanical fasteners were the go-to solutions for ensuring battery integrity, but their efficacy is often limited. Enter adhesives and sealants. These are not just bonding agents; they are the unsung heroes ensuring that batteries are not only more secure but also more sustainable.
In this comprehensive article, we’ll explore how adhesives and sealants are redefining the parameters of safety and ecological responsibility in the battery industry. We will delve into specific technologies, compare traditional and modern approaches, and touch upon the regulatory landscape shaping these changes. By the end of this read, you’ll grasp why adhesives and sealants are integral to pushing the battery industry toward a safer, more sustainable future.
The Growing Importance of Battery Safety and Sustainability
As the world shifts toward renewable energy and electric mobility, batteries are becoming ubiquitous in everyday life. In 2019, the global battery market was valued at $108 billion, and it’s projected to reach $152.3 billion by 2025, according to a report by Mordor Intelligence. This burgeoning demand amplifies the need for batteries that are not only efficient but also safe and eco-friendly.
Battery-Related Incidents: A Call to Action
Safety issues surrounding batteries have been well-publicized. From smartphones catching fire to electric vehicle (EV) battery meltdowns, incidents have raised concerns among consumers and regulators alike. In fact, the U.S. Consumer Product Safety Commission reports that in 2020 alone, over 25,000 battery-related incidents occurred, marking a 10% increase from the previous year. This alarming trend underscores the urgency to enhance battery safety measures.
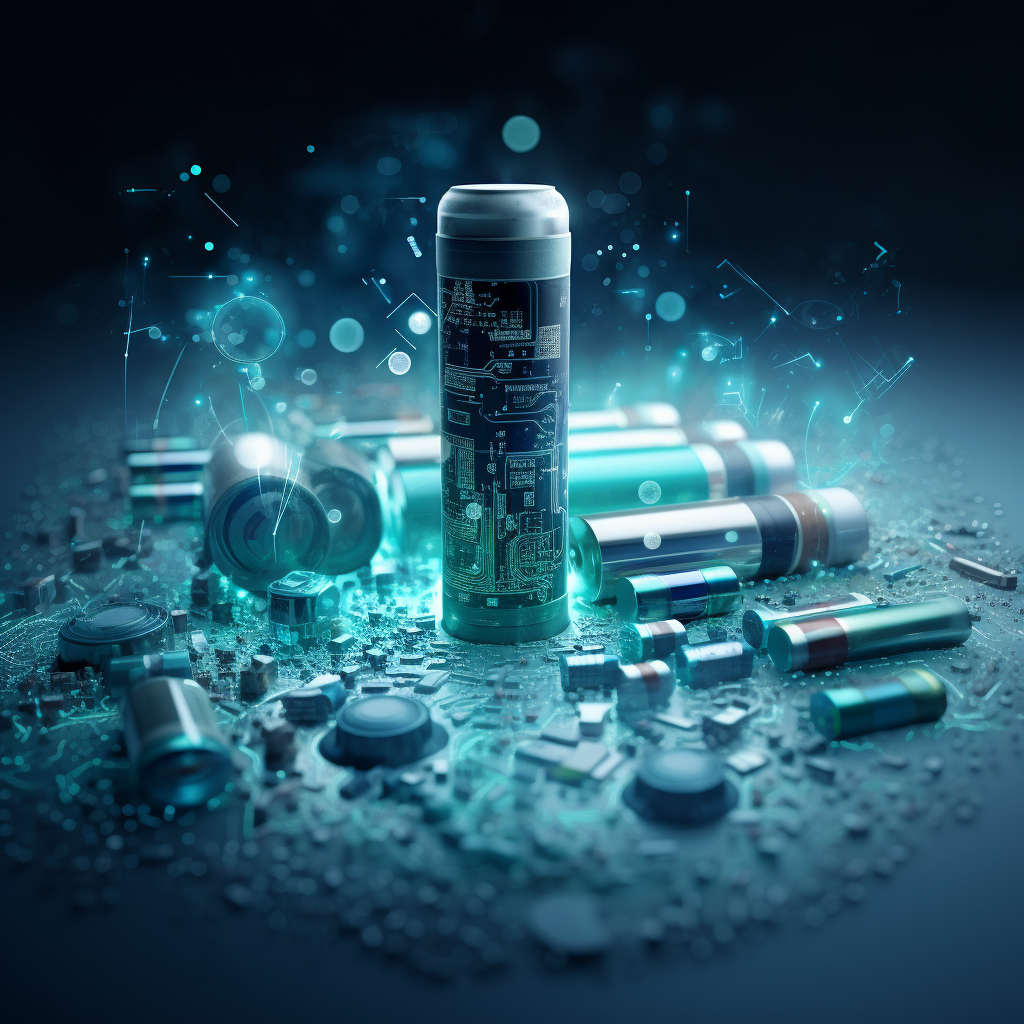
The Sustainability Quandary
Alongside safety, sustainability remains a vital concern. As per a study published in “Nature Sustainability,” the battery industry accounted for 800,000 tons of global carbon emissions in 2020. The environmental impact doesn’t stop at carbon emissions—many batteries contain toxic elements like cadmium and lead, which can contribute to soil and water pollution when improperly disposed of.
Dual Objectives: Safety and Sustainability
Given these twin challenges, there’s an impetus to innovate in ways that advance both safety and sustainability. The rise of electric vehicles, renewable energy storage, and portable electronics has necessitated batteries that are durable, efficient, and ecologically sound. Combining these attributes is a complex endeavor that calls for an interdisciplinary approach, one that involves material science, engineering, and regulatory oversight.
Traditional Approaches vs. Modern Solutions
Navigating the labyrinthine demands of battery safety and sustainability requires a multi-faceted strategy. However, as technologies evolve, so must the methods used to ensure their safe and efficient operation. Here, we evaluate the pros and cons of traditional approaches and explain why adhesives and sealants have emerged as essential tools in the modern battery landscape.
Mechanical Fasteners: A Tried and True Method
For years, mechanical fasteners like screws, bolts, and clips have been the standard choice for securing battery components. These methods have the advantage of being well-understood and easily reversible, allowing for repairs and parts replacement. However, mechanical fasteners also come with a host of downsides:
- Weight: Added material can make batteries heavier, affecting overall efficiency, especially in electric vehicles.
- Inconsistency: Uneven pressure distribution can create stress points that may weaken the structural integrity over time.
- Space: Fasteners require extra room, limiting design freedom and increasing the size of the battery pack.
The Rise of Adhesives and Sealants
With the evolution of battery technologies, the role of adhesives and sealants has become increasingly vital for several reasons:
- Uniform Distribution: Unlike fasteners, adhesives can distribute stress evenly across the bonded area, reducing weak points.
- Thermal Management: Specialized adhesives can dissipate heat effectively, thereby reducing the risk of overheating.
- Space-Efficiency: Adhesives and sealants allow for slimmer, more compact designs, catering to the shrinking sizes of modern electronics.
- Environmental Benefits: Certain adhesives are formulated from sustainable materials, offering eco-friendly advantages.
The Comparative Edge
When viewed through the lens of safety and sustainability, it’s evident that adhesives and sealants offer a compelling alternative to traditional methods. They are not merely a substitute but an upgrade, one that can meet the complex challenges posed by modern battery applications.
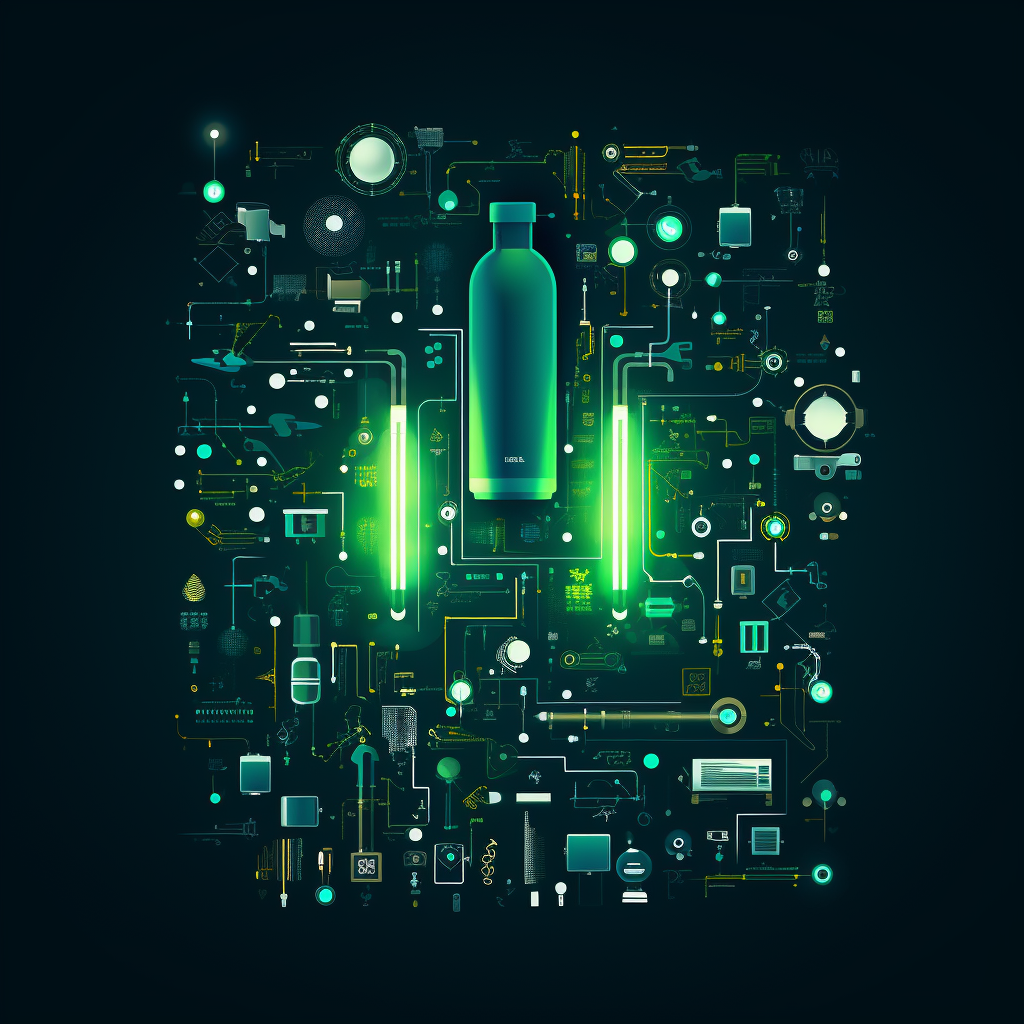
The Role of Adhesives and Sealants in Battery Safety
The increasing reliance on batteries across various sectors, from automotive to renewable energy, has brought the question of safety to the forefront. Adhesives and sealants have proven invaluable in addressing this concern, impacting multiple aspects of battery design and functionality.
Thermal Management
Heat buildup is one of the most significant safety risks associated with battery operation. According to the National Fire Protection Association, thermal runaway, a condition where an increase in temperature causes a further increase, resulted in 150 U.S. fire incidents involving lithium-ion batteries in 2020.
Adhesives can help mitigate this risk through effective thermal management. Thermally conductive adhesives disperse heat across the battery assembly, thus preventing hotspots that could trigger thermal runaway. Companies like Henkel and 3M have developed specialized thermally conductive adhesives designed explicitly for battery applications.
Structural Integrity
Battery packs are complex structures containing multiple cells and components. Any failure in structural integrity could result in a range of issues from performance degradation to safety risks. Adhesives, unlike mechanical fasteners, offer uniform stress distribution across the assembly. This even distribution reduces the risk of ‘weak points,’ which could compromise structural integrity.
Leak Prevention
Battery leaks are not just messy; they can be hazardous. Leaked electrolyte can be corrosive or toxic, posing risks to both the environment and human health. Sealants create an impermeable barrier that prevents such leaks, ensuring that the contents remain within the battery casing.
Safety Certifications and Adhesives
The Underwriters Laboratories (UL) has standards (such as UL 2054) that test the safety of household and commercial batteries. Adhesives and sealants that meet these stringent safety criteria offer an additional layer of assurance for both manufacturers and consumers.
In summary, adhesives and sealants are not just about bonding materials; they are crucial components that offer superior safety capabilities. Their contribution spans thermal management, structural integrity, and leak prevention—areas that are fundamental to battery safety.
Advancements in Adhesive and Sealant Technologies
In a landscape as dynamic as the battery industry, technological innovation is the driving force. Adhesive and sealant technologies have witnessed considerable advancements in recent years to cater to the specialized needs of modern batteries.
Specific Material Examples
- Epoxy Resins: These have become popular for their high thermal and electrical resistance. Companies like Dow and Sika have introduced epoxies that provide not just strong bonds but also durability under extreme conditions.
- Polyurethane Adhesives: Renowned for their flexibility and scalability, polyurethane adhesives are ideal for battery applications where thermal expansion is a concern. Products like Loctite’s UR-7000 series are engineered for this purpose.
- Silicone-Based Sealants: Known for their thermal stability, silicone sealants like those from Wacker Chemie AG provide an excellent barrier against moisture and corrosion, critical in harsh operating environments.
Case Studies
- Tesla’s Gigafactory: In producing lithium-ion batteries, Tesla employs advanced adhesives to meet the rigorous thermal and mechanical demands of electric vehicle applications.
- Duracell’s EcoAdvanced Batteries: Duracell has incorporated bio-based adhesives in their EcoAdvanced line, showcasing a drive toward sustainability alongside performance.
Custom Solutions
The customization of adhesives to suit specific applications is an emerging trend. Companies like H.B. Fuller offer tailor-made solutions that can meet the unique requirements of advanced battery technologies, including those used in aerospace and medical fields.
Reliability Testing
Ensuring that these advanced adhesives and sealants meet industry standards is essential. Extensive reliability testing, often exceeding ISO 9001 requirements, provides an additional layer of assurance in product efficacy and safety.
Advancements in adhesive and sealant technologies are not just incremental improvements; they represent leaps in the domains of safety and sustainability. Through material innovation and rigorous testing, these products are making significant contributions to the evolving narrative of battery technology.
Sustainability Through Material Choice
As the demand for batteries escalates, the environmental footprint cannot be overlooked. Manufacturers are increasingly aware that sustainability is not just a buzzword but a corporate responsibility. Adhesives and sealants are making inroads into this realm by offering eco-friendly options that align with sustainable manufacturing practices.
Eco-Friendly Options
- Bio-Based Adhesives: Made from renewable resources such as plant-based polymers, these adhesives are gaining traction for their reduced carbon footprint. Companies like Arkema have introduced bio-based adhesives that offer similar or better performance compared to traditional petrochemical-based products.
- Recyclable Adhesives: A focus on end-of-life recycling is crucial. Certain adhesive formulations can be more easily separated during recycling processes, thus facilitating better material recovery.
- Low-VOC Formulations: Volatile Organic Compounds (VOCs) are harmful both to the environment and human health. Low-VOC adhesives, like those offered by Henkel, minimize air pollution during the manufacturing process.
Lifecycle Assessments
Lifecycle assessments (LCAs) provide a holistic view of a product’s environmental impact from production to disposal. Some adhesives and sealants have undergone LCAs and have been proven to reduce the overall environmental burden when used in battery assembly.
Alignment with Regulatory Standards
Sustainable adhesive options often come with certifications such as ISO 14001 for Environmental Management Systems. Such certifications reassure manufacturers and consumers alike about the ecological soundness of these products.
Beyond Batteries
The adoption of sustainable adhesives isn’t limited to the battery industry. This eco-friendly shift is a part of a larger movement towards sustainable manufacturing across various sectors, including construction, electronics, and automotive.
In essence, the choices made in selecting adhesives and sealants have far-reaching implications for sustainability. Through conscious material selection, the battery industry can make significant strides toward reducing its environmental footprint. As we pivot to a more sustainable future, the role of adhesives and sealants in contributing to this change cannot be underestimated.
You may also like
-
Why Custom Software is Crucial for Scaling Your Business
-
Uncovering the Amazing Charm of Augmented Reality Technology!
-
AI for Good: Uncovering the Positive Impact on Society
-
The Future of Virtual Reality Slots: Immersive Experiences and Technological Advancements
-
Edge Computing: Transforming Internet with Optimum WiFi Plans