Wire Mesh vs Sintered Wire Mesh
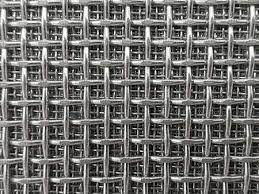
Both sintered wire mesh and traditional wire mesh find extensive use in many different contexts. While both consist of wires in some way, their properties, and uses are somewhat different. In this post, we’ll compare and contrast wire mesh and sintered wire mesh, looking at how their distinct features and potential uses affect the design process. Having a firm grasp of these components will equip you to pick the ideal mesh for your purposes.
What is Wire Mesh?
Wire mesh, often called wire cloth or wire netting, is a flexible textile made by weaving together individual wires. Individual wires are woven together in a crisscrossing, interlocking manner to produce this grid. Stainless steel, galvanized wire mesh manufacturers, aluminum, copper, and brass are just a few of the materials that can be used to make wires.
Properties of Wire Mesh
- The number of holes per linear inch defines the mesh size of wire mesh. It affects the mesh’s filtration or sieving capacities by dictating the mesh’s fineness or coarseness.
- The strength, longevity, and filtering effectiveness of wire mesh are all affected by the thickness of the wires used to create the mesh.
- Variations in Strength, Rigidity, and Filtration Accuracy depend on the Weave Pattern Options including plain weave, twill weave, and Dutch weave.
- Wire mesh’s open area percentage describes how many holes there are relative to the overall surface area of the mesh. The way fluids or gases move through the mesh is altered.
Applications of Wire Mesh
Filtration and Separation: Wire mesh is extensively used for filtration and separation applications in industries such as oil and gas, chemical processing, and water treatment.
Sieving and Sifting: Wire mesh screens are used for sieving and sifting processes to separate particles of different sizes in industries like agriculture and food processing.
Reinforcement: Wire mesh is employed as reinforcement in concrete structures to improve their strength and prevent cracking.
Protection and Safety: Wire mesh is used as protective barriers in fencing, security enclosures, and safety guards in industrial settings.
What is Sintered Wire Mesh?
Several layers of wire mesh are sintered together to create sintered wire mesh, also known as porous sintered wire mesh. In the sintering process, layers are fused together using heat and pressure to form a porous and solid whole. This produces a mesh with consistent pores, ideal for filtration and separation.
Properties of Sintered Wire Mesh
- Sintered wire mesh is excellent for filtering and separation because of its consistent pore diameters.
- Resistance to deformation and mechanical stress is enhanced by the sintering process, which also gives the mesh its high strength.
- Sintered wire mesh is suited for harsh industrial situations due to its resistance to high temperatures and corrosion.
- Sintered wire mesh is easily maintained because of its flat surface.
Applications of Sintered Wire Mesh
Fluid and Gas Filtration: Sintered wire mesh is widely used in fluid and gas filtration applications, such as in pharmaceuticals, petrochemicals, and water treatment. You may also check out Wire mesh filters suppliers in Delhi.
Porous Plates: Sintered wire mesh is used to create porous plates for gas diffusion and fluidization processes in chemical reactors.
Gas Diffusion: In fuel cells and batteries, sintered wire mesh is used for gas diffusion to facilitate efficient energy conversion.
Fluidization: Sintered wire mesh is employed in fluidized bed reactors to improve heat transfer and reaction efficiency.
Differences Between Wire Mesh and Sintered Wire Mesh
Manufacturing Process: Wire mesh is produced by weaving individual wires together, while sintered wire mesh is created by sintering multiple layers of wire mesh.
Porosity and Filtration Precision: Sintered wire mesh has uniform pores, resulting in precise filtration capabilities, whereas standard wire mesh may have varying pore sizes depending on the weave pattern.
Strength and Stability: Sintered wire mesh is stronger and more stable due to the sintering process, making it suitable for applications requiring mechanical strength.
Temperature and Corrosion Resistance: Sintered wire mesh offers better temperature and corrosion resistance compared to standard wire mesh. Also read here – https://dohaj.com/blog/
Cleanability: The smooth surface of sintered wire mesh allows for easier cleaning and maintenance.
Choosing the Right Mesh for Your Application
Consider the needs of your application before deciding between wire mesh and sintered wire mesh.
- Sintered wire mesh is the material of choice when consistent pore size and fine filtration/separation are required.
- Sintered wire mesh is recommended for uses that demand mechanical strength and resistance to high temperatures and corrosion.
- When a high level of accuracy is not required, wire mesh is an excellent choice for various filtering and separation applications.
Conclusion
Sintered wire mesh, like traditional wire mesh, is an indispensable material with several uses in numerous fields. Sintered wire mesh provides accurate filtering and great mechanical qualities, and wire mesh in general is versatile and flexible enough to be used in a wide variety of contexts. You can make an educated selection and select the optimal mesh for your requirements if you are familiar with its individual characteristics and potential uses. These meshes serve a significant role in improving the efficiency, performance, and safety of a wide variety of industrial processes, including sieving, filtration, and gas diffusion.